How the ETL certification process works
The ETL Mark is proof of product compliance to North American safety standards. Authorities across the US and Canada accept the ETL Listed Mark as proof of product compliance to published industry standards. Retail buyers accept it on products they're sourcing.
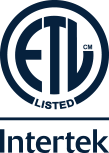
To have the right to bear the ETL mark, the product must have been tested by a Nationally Recognized Testing Laboratory (NRTL). A Nationally Recognized Testing Laboratory (NRTL) is an independent laboratory recognized by the American Occupational Safety and Health Administration (OSHA) to test products to the specifications of applicable product safety standards.
Today, Intertek has 14 test laboratories across North America, Europe and Asia that are formally recognized as NRTL sites, plus an additional 22 laboratories that are qualified to test products for North American (USA and Canada) certification under the umbrella of our headquarter NRTL site in Arlington Heights, IL.
This is what the ETL process looks like
1. Request for ETL Certification
To give you a quote, we will need the following information:
- Details of certification applicant
- Product specifications and models
- Description (intended use)
- Target user base
- Details of recognized /listed components or sub-assemblies (Read more)
- Details of manufacturer(s) and location(s)
2. Quote for testing and certification
The quote will include the following information:
- Applicable standard(s)
- Name of lab/reviewer
- Timeline (milestones)
- Price
- Unlisted components annual testing fee (Download ETL Certification Rates)
- Certification follow-up service fee (Download ETL Certification Rates)
3. Product testing
To perform product testing we will need the following from you:
- Test sample
- Technical documentation on the product. NB: For Canadian certifications bilingual cautionary marking requirements apply (Read more)
After the product testing is completed you will receive a copy of the Listing report/ Constructional Data Report (CDR), including information on production line testing. This report will be used by the inspector during the quarterly inspections. NB: You do not need to forward the Listing report/CDR to the certification department.
4. Certification
To complete the certification process, we need the following from you:
- Certification agreement (signed by you as applicant and the manufacturer(s) if the manufacturer is different from the applicant) (Download Certification Agreement).
- Filled out and signed Client Information Sheet (CIS) (Download CIS).
- Sample of your ETL label artwork (if you intend to print the ETL mark directly on the product, download more information here) or purchase order for ETL labels. (Download ETL Label Order Form).
- A copy of your company’s business registration papers to confirm your legal name. This is also known as your Certificate of Incorporation papers. This document would be issued by your government and shows your legal name and unique business identification number and will ensure that we are communicating with the correct company and that no proprietary information is given out to the wrong company.
Once completed, please email the documents to your test lab with cc: to etlrlceu@intertek.com
- Multiple Listee form if applicable – The Multiple Listing Service is used when identical products certified by Intertek to U.S. and/or Canadian requirements for one company are produced for marketing under the name of another company i.e the Multiple Listee. (Download Multiple Listee form).
Please email the completed document to your test lab with cc: to etlrlceu@intertek.com
5. Initial factory inspection
The Initial Factory Assessment is performed to ensure that your manufacturer’s internal processes are well-defined and appropriate for the manufacture of compliant products. In addition to the Initial Factory Assessment, an Initial Product Inspection (IPI) will be completed in order to verify that the product is in line with the descriptive Constructional Data Report (CDR) prepared by our engineering department. The CDR is a part of the certification document.
To prepare for the Initial Factory Inspection, please download our Initial Factory Assessment Checklist.
Production Line Testing
As a requirement for ETL certification the manufacturer shall conduct regular production line tests in the factory. Records of these tests will be checked during factory assessments. The CDR will specify if test are necessary and if so, which tests should be done. (Read more)
6. Authorization to Mark and ETL listing
Please note that you are not allowed to start labeling your products with the ETL mark until you have received a signed and dated "Authorization to Mark". The "Authorization to Mark" (ATM) can only be issued after a successful Initial Factory Assessment.
7. My Testcentral
My TestCentral is an online archive of ETL Listing reports. Stored in a highly secure portal environment, your reports will only be viewable to users you choose. You maintain total control over who can access your reports. Registration is easy, fast, and free.
8. Maintenance and follow-up services
This includes:
- Unannounced Quarterly Factory Inspection (Follow-up Service). Refer to Certification Agreement clause 3.3 (Read more)
- Standard update notices
- Annual unlisted component testing (Read more)
- Quarterly inspections and follow-up fees (Read more)
What we need from you:
A continuous dialogue – any changes in ETL listed products must be reported to us at etlrlceu@intertek.com
9. Variations
In the ETL mark context, there are three kinds of variations:
1.Variations found during inspections
What are they?
They are discrepancies between the actual product and the ETL Listing Report found during either the Initial Factory Assessment or during quarterly follow-up inspections.
How do we inform you of these variations?
Variations found during the Initial Factory Assessment (IFA) are stated in the inspection report, which is left with the manufacturer after the inspection has been completed.
Variations found during a quarterly follow-up inspection are stated in an inspection report, which is left with the manufacturer after the inspection has been completed.
What do you need to do and what happens if you fail to comply?
Initial Factory Assessment (IFA) variations
To be authorized to ship products bearing the ETL mark, the Initial Factory Assessment (IFA) must be approved. Therefore, you must respond to variations found during the IFA as soon as possible and your response must include all necessary supporting technical documentation. If a revision of the ETL Listing report is needed to solve the variation, your response should include which engineering office you have contacted as well as contact name and date of contact, quotation, date of accepted quotation and job number as applicable.
If we do not receive your response within 6 months, the ETL Order number will be terminated due to no approved Initial Factory Assessment (IFA).
Follow-up inspection variations
Variations are to be responded to within 15 working days of the inspection date. Variations should be solved within 3 months (before the next inspection).
If you do not respond to variations or are unable to show evidence during inspection that the variations are being resolved, the applicable ETL Listing report will be suspended until the variation has been resolved. If variations are not resolved, your ETL Listing will be terminated.
2. Variations regarding standards
What are they?
Discrepancies between the requirements in the applicable standard, the actual product and the ETL Listing report due to standard updates.
How do we inform you of these variations?
When a new or revised standard is published, we issue a Standard Update Notice-document (SUN) detailing the changes to all concerned.
What do you need to do and what happens if you fail to comply?
The Standard Update Notification (SUN) document has an Effective Date, by which the applicable ETL Listing report(s) must be revised according to the new standard requirements and show the new standard information.
If you fail to update your ETL Listing report accordingly, the Listing report will be terminated as it is no longer compliant with the applicable standard.
3. Variations regarding Unlisted Components
What are they?
When Unlisted Components used in a certified product fail mandatory annual testing.
How do we inform you of these variations?
In the beginning of every year, we issue a notification called a Selection-Letter Evaluation-email to clients using Unlisted Components in their products. This notification specifies which components need to be submitted for retesting that year.
After completed Unlisted Component testing, a report is issued by the applicable Component Evaluation Center (CEC) or Engineering office (whichever is applicable). The report can be either an acceptance report (all good, testing OK) or a Discrepancy report (something does not comply, there are variations), also called a UC-FAIL.
What do you need to do and what happens if you fail to comply?
If you receive a UC FAIL report, you need to take appropriate corrective action immediately. An email detailing the actions you propose to take should be sent to svn.europe@intertek.com within 30 days from the date of the UC FAIL report. If you take no or insufficient corrective action, your ETL Listing report will be suspended and eventually terminated.